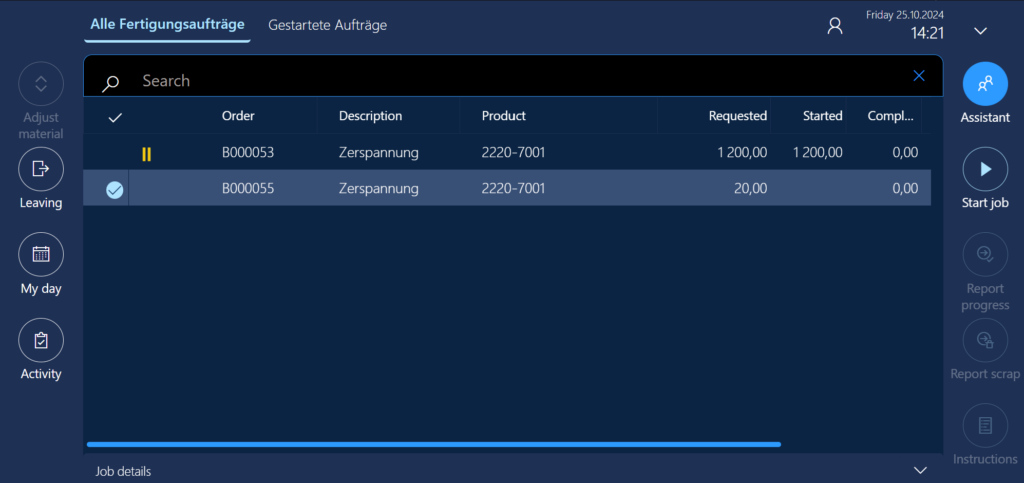
Assistance and Secondary operations in D365 for SCM to separate machining costs from labour
In Dynamics 365 Supply Chain Management (SCM), in its recent internal MES incarnation called “Production Floor Execution” (PFE), there is a notion of Assistance.
The Assistance model helps solve a controlling challenge: recording machine costs and labour costs separately. For example, setting a machine up consumes less energy than a full speed machine operation: during the setup job, the labour cost prevails if we neglect the amortization. On a contrary, once a highly automated work cell is programmed and set up, the worker may leave and let the cell run on its own. The machine cost prevails. Consequently, instead of a blended rate of the machine hour, we may decide to split the hours into 2 different route categories: one for the machine, one for the worker, and even one more for the energy consumption.
Assistance is when multiple workers share one job. A lead worker (pilot) is assigned the production order job, and other workers join as assistants. The Pilot’s time is replicated into the Assistant’s time records, thus increasing the labour cost per item: N workers : 1 order.
In contrary, if workers handle several production orders at once it is called bundling. This mode shares labour costs across orders, lowering the cost per item: M orders : 1 worker. In a general case, the relation between the orders and workers may be M:N, if a team of assistants takes on a bundle of production orders.
Primary vs. Secondary operations
In Dynamics 365, production steps are called operations. Some operations are “primary”, meaning they control the main task, usually involving a machine or workstation. Others are “secondary”, like additional labour or support roles, running alongside the primary task. Primary and secondary operations share the same operation number but have different Operation IDs in Dynamics 365. They both run at the same time, and the primary operation controls how long the job lasts.
Setting up secondary operations for labour cost tracking
- Define distinct Production control > Setup > Routes > Cost categories for the machining and for the labour.
- In Production control > Setup > Routes > Route groups, create one group and activate the Setup and/or Process jobs appropriately. Check Job management and Capacity to make the jobs visible on the PFE terminal. Turn on the Setup time and/or Run time estimation and costing.
- Define secondary operations in the Route: specify the main machine task as the primary operation and the labour support task as the secondary.
- In Production control > Setup > Manufacturing execution > Configure production floor execution, choose Design tabs and make sure the button (Action) “Assistant” is placed onto one of the toolbars.
- Check if the system jobs Start assistance and Stop assistance exist under Time and attendance > Manage indirect activities > Indirect activities. Use Time and attendance > Setup > Wizards > Time and attendance configuration wizard if they don’t.
- Go to Production control > Setup > Manufacturing execution > Production order Defaults and check Assistants use secondary operations on the Operations tab. This setting lets assistants’ time be logged under the secondary operation, ensuring correct labour cost tracking.
- Make sure a dummy worker representing the machine exists alongside the real machine operator and they are activated for Time registration in the Time and attendance > Setup > Time registration workers.
- With the setup in place, Release a test production order.
- Open the Production control > Manufacturing execution > Production floor execution terminal, perform the initial configuration if needed. Choose the machine ID as a filter for the production jobs.
- Clock in the machine first with its fictive Badge ID. The PFE terminal opens the list of the primary jobs planned at the machine as shown on the screenshot above.
- Let the machine “Start job“.
- In a “shared terminal” scenario such as ours, the PFE terminal usually immediately logs the user=machine off, otherwise click Leaving / Log off.
- Log in as a human worker (machine operator) with your own Badge ID.
- Use the Assistant button on the PFE terminal to “attach” yourself as an assistant to the Pilot=machine.
- You will see a “You are now registered as an assistant” message right after. The machine becomes the “pilot”.
- Check Time and attendance > Inquiries and reports > Teams: there is now a Job pilot driving the primary operation and an assistant Worker attached to it.
The Resource pilot in this form is a remnant of a nice feature Assist Resource. The Assist Resource was supposed to be a machine or a similar asset acting as the Pilot instead of a dummy machine worker, making it simpler to track time. However, the corresponding button "Assist resource" is defunct on the modern PFE terminal: the necessary twin action "Start resource jobs" from the legacy Job card terminal is not implemented in the Production floor execution, so the Assist resource does not do anything useful.
- Check the time records of the day in the Time and attendance > Review and approve > Approve list: a Start assistance line has been recorded for the worker. The T&A module is quietly listening to everything what the pilot does:
- After a while, Clock out the human worker.
- Check the time records in Time and attendance > Review and approve > Approve: the T&A module has now copied all the records of Pilot=machine to the Assistant during the active assistance period, yet the Process Job ID is not the same, it is the one of the secondary operation with its distinct cost rate! This does not work properly if you register route operations instead of jobs. Specifically, a Job level = Route is a no-go in Production order defaults.
- Check Time and attendance > Inquiries and reports > Teams again: the team is disengaged. If the worker mostly serves the same machine, you may activate Permanent teams in the Production control > Setup > Manufacturing execution > Manufacturing execution parameters. This will auto-attach the human worker to the machine on subsequent clock-ins.
- At the end of the shift, assistants must clock out first: the Pilot can’t clock out until all assistants have done so. Indeed, you may now Clock out the machine.
Separate energy cost
Production and Manufacturing blog series
Further reading:
Integrate APS with Dynamics 365 for SCMD365 Mass de-reservation utility
Picking list journal: Inventory dimension Location must be specified
Consumable “Kanban” parts in D365 Warehouse management
Subcontracting with Warehouse management Part 2
Subcontracting with Warehouse management Part 1
Semi-finished goods in an advanced warehouse
The case of a missing flushing principle
2 Comments
Great solution! How to start secondary operation (labor) automatically? I have tested it and i’ m not able to complete (report as finished) the production order if I don’t start manually the secondary one operation. Thanks
The idea of the assistance is to start the secondary op. manually and to record a different working time. If you only wish to post Xth type of cost separately, see the section about the energy and start booking the time automatically based on the reported quantity, for example.